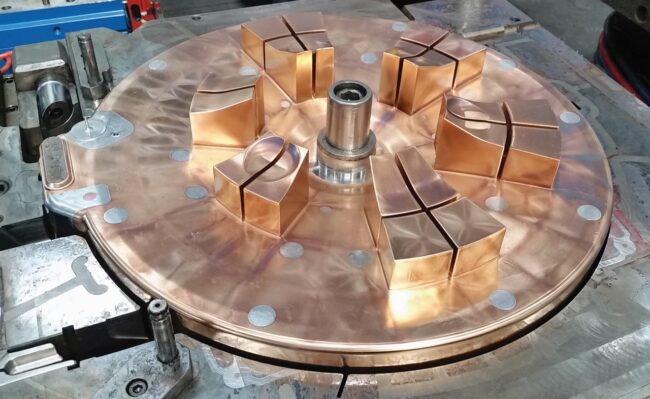
Manufacturers understand inherent time losses in production, such as molten plastic cooling within injection moulds. While water circulation helps this process, there’s often room for improvement. This article examines a crucial factor that’s often overlooked – the material of the injection mould itself.
The importance of thermal conductivity
Different materials possess varying thermal properties. When cooling plastic, thermal conductivity becomes paramount. The higher the conductivity, the faster the heat transfer and mould cycle times. Iron, a common mould material, offers limited conductivity (60 W/m K), while other options excel.
Copper alloys: The superior choice
Copper alloys boast impressive thermal conductivity, averaging 399 W/mK. This surpasses aluminium by 60% and stainless steel by a staggering 3000%. Furthermore, copper alloys combined with elements like beryllium, nickel, silicon, and chrome provide optimal blends of hardness, wear resistance, and thermal fatigue alongside outstanding conductivity. Beyond conductivity, it has additional advantages as follows:
- Reduced polishing time: Copper alloys exhibit exceptional polishing ability, demonstrated in contact lens packaging production. Copper alloy inserts achieved four times faster polishing than steel, leading to a 57% cycle time reduction.
- Minimised warpage: Improved cooling allows moulded components to spend less time at high temperatures, reducing “hot spots” and warpage, resulting in consistent part quality.
- Efficient heat removal: High conductivity effectively draws heat away from sensitive areas, often eliminating the need for complex cooling channels. This reduces machining costs by upto four times compared to steel moulds.
- Heat diffusivity: Copper alloy moulds excel in heat diffusivity, swiftly drawing heat away from plastic. This extends cooling time, leading to shorter cycles and reduced plastic warping.
- Coating options: For enhanced wear resistance, copper alloys can be readily coated with electroless nickel, hard chrome, or PVD coatings. Electroless nickel provides superior coating consistency than galvanic processes, like hard chrome plating. Additionally, electroless nickel can be combined with Teflon or boron nitride for effortless demoulding.
Unlocking efficiency
While cost constraints often lead to conventional steel moulds, high- conductivity copper alloys offer substantial long-term benefits. Manufacturers seeking to optimise production with faster cooling, reduced warpage, efficient heat removal, and improved polishing should seriously consider the advantages of investing in these high- performance materials.
COMMENTS