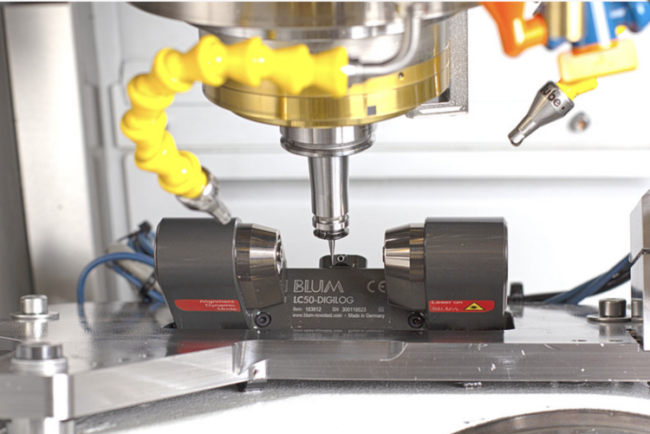
Reliable measurement of 10 µ tools
When it comes to carbide tools, there are always products that push the boundaries of what was previously considered technically possible. Some of these incredible products are made by ZECHA Hartmetall-Werkzeugfabrikation GmbH – for instance, a two-flute end mill with a diameter of 10 µ or a PCD tool that has 42 cutting edges with a diameter of 6 millimetres. However, the company from Königsbach-Stein in Germany not only makes tools, but also supplies complete solutions for manufacturing processes. It is here that laser measuring technology from Blum-Novotest plays an important role.
ZECHA tools are used in many different industries, which means the company is quite resistant to crisis: The customer products range from mould and tool construction, dental and electrical engineering to the pharmaceutical, textile, furniture, jewellery, automotive and aerospace industries. The company specialises in tools with diameters from 12 mm to very small micro-tools with diameters of 0.01 mm with the highest level of precision. Manufacturing these tools requires a high degree of expertise, because the geometries of normal-sized tools cannot simply be scaled down to the micro range. When milling cutters with a diameter of a few tenths of a millimetre are used, the machining conditions are completely different from those for conventional dimensions.
“But our product range goes far beyond tools”, emphasises product manager Stephen Rapp. “We supply complete solutions for machining applications, and work closely with machine and accessory manufacturers in the process. This is because we don’t just provide customers with tools, but also with a production process that is customised to their machines if needed”.
This leads to the question of how to measure such small tools, which are many times smaller than a human hair, and how to ensure that the machining process is reproducible. “It is especially important that the measurement is done in the machine, because this is the only way to record and compensate for all influencing factors. Since machine manufacturer KERN has been integrating laser measuring systems from BLUM into its precision machines as standard for many years and ZECHA has its own high-end machine, it didn’t take long to decide on the LC50-DIGILOG”, says Marcus Becker, milling application engineer at ZECHA, looking back at the project. “After initial system tests, it was immediately clear that the BLUM product was perfect for measuring micro-tools, even though they measure only 10 micrometres in diameter”.
In 2017, BLUM introduced the LC50-DIGILOG, a new generation of laser measuring systems that featured the revolutionary DIGILOG technology for the first time. When it came to precision, measuring speed and process reliability, it outshone everything that had come before. In contrast to conventional laser systems that generate a single measured value when the laser
beam is shaded to a certain degree, the LC50-DIGILOG laser measuring system determines the actual measured value based on thousands of individual values per second. “In addition, thanks to the large number of measured values per cutting edge, this intelligent system detects contamination and cooling lubricant deposits on the tool and calculates them out of the result, which makes the measurement results even more reliable”, explains Kai Fundel, sales technician at Blum-Novotest. “Combined with many other improvements such as the perfected laser optics, an optimised beam shape and the 30 percent reduction in the focus diameter, we allow for absolute accuracy beyond all comparable measuring systems”.
Unsurprisingly, in addition to tool measurement, tool breakage detection is also an important issue with micro-tools and, when it comes to 10 µ tool, is even crucial for process reliability. The probability of tool breakage is naturally much higher here than with standard tools and, without the laser measuring system, it could only be detected if machining was not completed. This is where non-contact measurement at machining speed, which is made possible with the DIGILOG system from BLUM, offers great advantages, as it is done in a matter of seconds and is absolutely reliable without the risk of damaging the tool.
The LC50-DIGILOG also plays a major role in process development for customers: “With the LC50-DIGILOG, we are able to precisely measure service life and wear in new processes or newly developed tools. After all, our customers want to know what tool life they can expect before they buy”, reports Marcus Becker. “A big advantage here is that the laser measuring system is not limited to micro-tool technology, but covers all of our tool diameters. This means we can develop all processes with one measuring system”. Even different coating colours have no effect on measurement results. Together, the specialists from ZECHA and BLUM measured the entire tool range for the test and achieved the best measured values without fail.
Along with the laser measuring systems, ZECHA also uses the LC-VISION software from Blum-Novotest. This is a measuring and visualisation software that can be used to quickly and easily generate, visualise and evaluate a wide variety of measurement applications on the control screen. “The ‘stability function’ in LC-VISION, for instance, allows us to get to know the behaviour of the machine, to put it simply. You can see relatively quickly when the machine has reached a stable thermal state and can start the machining process”, explains Marcus Becker. “However, I would also like to emphasise how user friendly the LC-VISION measuring software is, because it offers more options and is more convenient than when the measuring processes are called up and performed via an NC cycle. The software offers evaluations for many measurement series, a dashboard that shows wear trends, as well as other factors, and intuitive creation of measurement programs for a wide range of tools”.
Whether visualisations of the measured tool contour to assess breakouts or statistics for long-term tests are needed, LC-VISION also provides a wealth of useful information during tool development. “For instance, to assess our own manufacturing processes, we use single cutting edge measurement, when all the cutting edges of a tool can be measured and compared to each other. And this also applies to tools with a diameter of just 10 µm”, emphasises Thilo Hutmacher from the ZECHA Research and Development department. “Especially with very small tools, concentricity is of great importance; in the worst-case scenario, an imbalance is enough to cause the tool to break at nominal speed. That means measurements in the machine, with the spindle running and in the tool holder, are extremely important for us, because the entire system is measured, not just individual components”.
ZECHA is now presenting its customers with complete packages consisting of tool, process and DIGILOG laser system. These ensure high machining quality and guarantee the best possible productivity. Breakage detection after each machining step protects the machine and downstream tools – it is essential for trouble-free unmanned operation. The high-quality tools can also be used up to their individual wear limits instead of being replaced after a specified service life impacted by safety factors. “The LC50-DIGILOG also allows us to ensure process reliability down to the µ range. We are now in constant contact during process development, which means we can offer our customers the best possible solutions”, explains Marcus Becker. “The DIGILOG system is also very good when it comes to measuring speed. A normal measurement only takes a few seconds, while other technologies require multiples of this time with less accuracy. After all, we are always looking for the last ‘µ’ – with BLUM, we’ve found a partner that ticks just like we do”.
COMMENTS