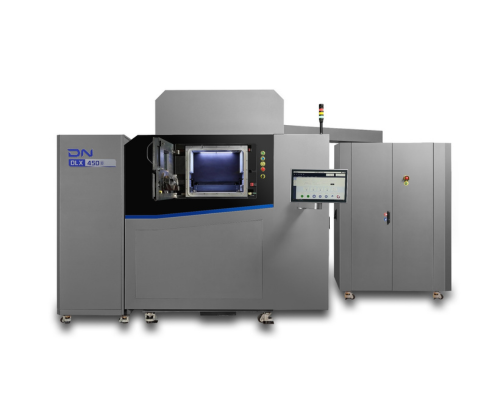
DN Solutions (formerly Doosan), will unveil its new DLX series at EMO Hannover, taking place from September 22 to 26, 2025. With the introduction of a metal 3D printer to its product lineup, DN Solutions is combining additive and subtractive manufacturing for the first time—offering a complete, end-to-end production solution. This powerful synergy between 3D printing and CNC technology enables the creation of highly complex components in significantly reduced production times.
The DLX series marks DN Solutions’ global entry into the fast-growing additive manufacturing market. With its first industrial-grade LPBF metal 3D printer, the company is targeting applications that push beyond the limits of traditional manufacturing—such as lightweight structures, organic geometries, and function-optimized metal parts. When integrated with established machining processes, this metal 3D printer supports the entire production chain, opening up new possibilities in high-performance, hybrid manufacturing.
The goal is to bridge the previously missing end-to-end link between LPBF and CNC processes. By systematically integrating software, automation, and component handling, DN Solutions lays the foundation for scalable turnkey solutions across the entire manufacturing process.
The flagship of the new Additive Manufacturing division is the DLX 450D. The industrial high-performance 3D printer is suitable for 24/7 production and offers an exchangeable build container to minimize non-productive time, a multi-laser system for high printing speed and a build volume of 450 × 450 × 450 mm.
Additive manufacturing, and the machines in the DLX series, help shorten time-to-market for new products, reduce costs through component integration, and enable innovative designs—ranging from complex geometries and lightweight structures to internal near-contour cooling channels and highly customized parts. The metal 3D printer serves key industries such as aerospace, automotive, semiconductor manufacturing, and medical technology.
Ahead of the official market launch, DN Solutions successfully tested the technology by redesigning the front cap of a spindle cylinder for the multitasking machine DNX2100, applying Design for Additive Manufacturing (DfAM) principles. The result: a 20% performance improvement and simplified assembly through integrated component design.
“In our view, there is no alternative to additive manufacturing for companies that want to produce competitively. It offers opportunities to produce complex metal components that could not be realized otherwise,” says Vino Suntharakumaran, Vice President Additive Manufacturing, DN Solutions. “It was therefore a logical step for as a holistic solution provider to include this technology in our portfolio. The mandatory mechanical post-processing allows us to utilize synergies of already established technologies such as five-axis simultaneous machining and automation solutions. In addition to these solutions, we complete the 360° offering with software, services and support. This ranges from consulting on what to print and how to design for additive, to training and ramp-up support during production, directly on site.”
DN Solutions also provides support along the additive process chain with its in-house AM software suite – from the initial idea to the design and the successful production of the component. The integrated approach of hardware and software is particularly helpful for companies that want to get into additive metalworking or expand their production. In future, customers will receive support at the Additive Solution Center in Gütersloh, which will open in 2026.
“Silver & Blue”: Exhibited machines show award-winning design concept. In addition to the new DLX series, DN Solutions will be exhibiting further machines from the “DN Solutions Universe” at EMO, including the DVF5000 2nd Generation and the DNX2100. Both machines have undergone significant design updates and are the first to be launched on the market in the new Red Dot Award-winning product design. The 5-axis machining centers of the DVF series reduce setup times and increase productivity, especially in demanding industries such as aerospace or the semiconductor industry. At the same time, the DVF machines in combination with automation solutions allow for the realization of unmanned systems. The DNX series, a multi-axis solution and compact multitasking machine, machines complex workpieces and has recently become available with the machine control system Siemens Sinumerik One.
COMMENTS