
In today’s rapidly evolving manufacturing landscape, optimizing material utilization is no longer a choice but a necessity. As industries worldwide strive to strike a balance between sustainability and profitability, efficient use of raw materials has emerged as a key factor in ensuring long-term success. For manufacturers involved in sheet metal forming, minimizing material waste while maintaining production efficiency is critical to achieving cost savings and environmental responsibility.
With increasing pressure from regulations, rising raw material costs, and the need for sustainable manufacturing practices, companies are looking for advanced solutions to enhance material efficiency. Sheet metal simulation software has proven to be a game-changer in this domain, enabling manufacturers to optimize blank utilization, reduce scrap, and enhance process accuracy. This article explores the various aspects of material utilization in sheet metal forming, the challenges involved, and how modern simulation technologies can help businesses achieve both sustainability and profitability.
The Importance of Material Utilization in Sheet Metal Forming
Material utilization in sheet metal forming refers to the efficient use of raw materials to produce components with minimal waste. This efficiency directly impacts both the cost-effectiveness of production and the environmental footprint of a company.
Cost Savings through Optimized Material Use
Raw materials account for a significant portion of manufacturing costs. Poor material utilization leads to excessive scrap, which not only increases costs but also necessitates additional handling and disposal efforts. By optimizing material usage, manufacturers can reduce per-unit costs and enhance profitability.
Environmental Impact of Waste Reduction
Manufacturing waste contributes to environmental degradation, increasing landfill accumulation and resource depletion. Efficient material utilization reduces scrap generation, thereby lowering energy consumption and minimizing carbon emissions associated with material processing and disposal.
Maximizing Output from Raw Materials
Optimizing material utilization enables manufacturers to produce more components from the same amount of raw material, increasing production efficiency. This is particularly crucial in industries that use high-value materials such as aluminium and stainless steel, where waste can be expensive.
Challenges in Achieving High Material Efficiency
Despite its significance, achieving optimal material efficiency in sheet metal forming comes with several challenges:
Design Complexity and Material Wastage
Sheet metal components often have complex geometries, requiring intricate cutting patterns that can result in high levels of waste. Traditional cutting and forming methods may not be optimized for material efficiency, leading to excessive scrap.
Variability in Material Properties
Sheet metal materials exhibit variations in thickness, strength, and elasticity, affecting formability. Inconsistent material properties can result in defects such as wrinkles, cracks, and springback, leading to rework and material wastage.
Trial-and-Error Approach in Tooling and Die Design
Conventional sheet metal forming relies heavily on physical prototyping and trial-and-error adjustments in tooling design. This approach is not only time-consuming but also results in unnecessary material usage.
How Sheet Metal Simulation Software Enhances Material Utilization
Modern sheet metal simulation software has revolutionized the way manufacturers approach material utilization. By leveraging computational modeling and predictive analysis, these tools help minimize waste and optimize production efficiency.
Blank Size Engineering and Nesting Optimization
One of the most effective ways to reduce scrap is through blank size engineering and nesting optimization. Simulation software allows manufacturers to determine the optimal blank shape and layout for maximum material efficiency. By arranging multiple parts strategically on a sheet, blank nesting optimization minimizes the amount of raw material required for production.
Predicting and Preventing Defects
Simulation tools enable manufacturers to predict defects such as thinning, wrinkling, and tearing before actual production. By identifying potential issues early, manufacturers can adjust tooling and process parameters to prevent material waste due to defective parts.
Virtual Prototyping Reduces Material Waste
Traditional prototyping involves multiple iterations, consuming excess material and time. Virtual prototyping allows manufacturers to test different process scenarios digitally, optimizing designs before actual production, thereby reducing scrap generation.
Advanced Material Selection for Better Utilization
Choosing the right material is crucial for optimizing material utilization in sheet metal forming. Simulation software plays a vital role in this process by analyzing factors such as formability, strength, and cost-effectiveness. High-strength materials allow manufacturers to reduce the amount of material required for a given application while maintaining structural integrity. By leveraging advanced simulations, manufacturers can determine the most suitable material for specific forming processes, ensuring minimal waste and maximum efficiency. The ability to predict how different materials will behave under various forming conditions helps in making informed decisions, reducing trial-and-error in material selection.
Another innovative approach to material utilization is the implementation of multi-material forming strategies. By combining different materials, manufacturers can optimize strength and weight distribution while minimizing excess material usage. Simulation software enables the analysis of hybrid forming techniques, allowing manufacturers to achieve enhanced performance with reduced raw material consumption. This strategic selection and combination of materials not only improve product quality but also contribute to sustainability by reducing overall resource usage in the manufacturing process.
Optimizing Tooling and Die Design for Reduced Waste
Tooling design plays a crucial role in material utilization, directly impacting efficiency and waste reduction in sheet metal forming. Simulation software helps refine die designs by optimizing material flow, minimizing defects, and ensuring better part accuracy. By analyzing different tooling configurations, manufacturers can improve material usage efficiency while reducing the need for excessive trial-and-error adjustments. This not only saves raw materials but also lowers production costs and enhances overall process stability.
One of the key advantages of simulation-driven tooling design is the ability to optimize die geometry. By accurately predicting die performance, manufacturers can create tools that maximize material utilization while maintaining high-quality production standards. Additionally, simulation software helps reduce tooling errors and the need for frequent manual adjustments. By identifying potential issues before production begins, manufacturers can lower material waste, improve overall efficiency, and extend tool life—leading to a more sustainable and cost-effective manufacturing process.
Economic and Environmental Benefits of Improved Material Utilization
Improving material utilization has both economic and environmental advantages:
- Cost Reduction: Less material waste leads to significant cost savings.
- Sustainability: Reduced raw material consumption lowers carbon emissions and energy use.
- Regulatory Compliance: Efficient material use helps manufacturers comply with environmental regulations.
- Enhanced Competitiveness: Companies that optimize material utilization gain a competitive edge by offering cost-effective and sustainable solutions.
Future Trends in Material Utilization for Sustainable Manufacturing
As manufacturing moves towards greater efficiency and sustainability, emerging technologies are transforming how material utilization is optimized in sheet metal forming. One of the most impactful advancements is Digital Twin Technology, which creates virtual replicas of production processes to enable real-time monitoring and optimization. By simulating and analyzing forming operations before physical production begins, manufacturers can identify areas of material waste, test process improvements, and refine designs with minimal resource consumption. This predictive approach ensures that material utilization is maximized while reducing costly errors and inefficiencies.
Another key trend shaping the future of material utilization is the adoption of sustainable and circular manufacturing practices. More manufacturers are shifting towards a circular economy, where materials are recycled and reused to minimize waste and environmental impact. Strategies such as closed-loop material recovery and remanufacturing help reduce raw material dependency while improving cost efficiency. Additionally, the integration of AI and big data analytics is set to revolutionize material utilization by predicting process inefficiencies and recommending real-time adjustments. AI-driven insights enable manufacturers to make data-backed decisions, optimize material flow, and continuously refine production processes—ensuring both profitability and sustainability in the long run.
Conclusion
Optimizing material utilization in sheet metal forming is critical for manufacturers aiming to achieve both sustainability and profitability. By leveraging advanced simulation software, companies can reduce waste, enhance efficiency, and minimize costs. The adoption of AI-driven automation, digital twin technology, and optimized material selection will continue to revolutionize the industry, helping manufacturers strike the perfect balance between economic success and environmental responsibility. Embracing these innovations will not only improve production outcomes but also position companies as leaders in sustainable manufacturing.
As industries evolve, those who prioritize material utilization will stay ahead of the competition, benefiting from lower production costs, higher resource efficiency, and a reduced environmental footprint.
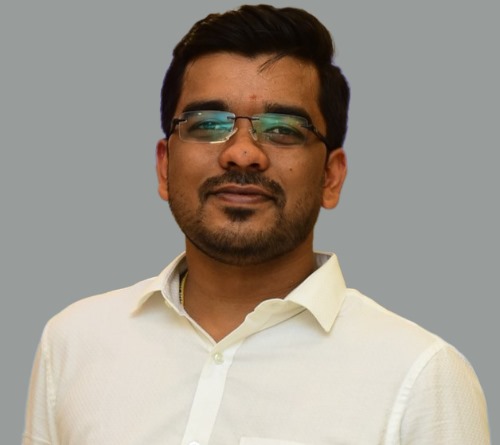
Akshay has completed Masters in Tool Design and has accumulated over a decade of experience in the field of stamping tooling while working with several major tool manufacturers. As a Product Manager for Dynaform, he focuses on enhancing Dynaform to meet evolving market demands, advance sheet metal technology, and exceed user expectations.
COMMENTS