Precision machining is an indispensable tool in the hands of skilled die makers. Its ability to create highly accurate, complex, and durable dies is crucial for the production of high-quality parts in various industries. As technology continues to evolve, the role of precision machining in die making will undoubtedly become even more vital and transformative.
Sudhanshu Nayak
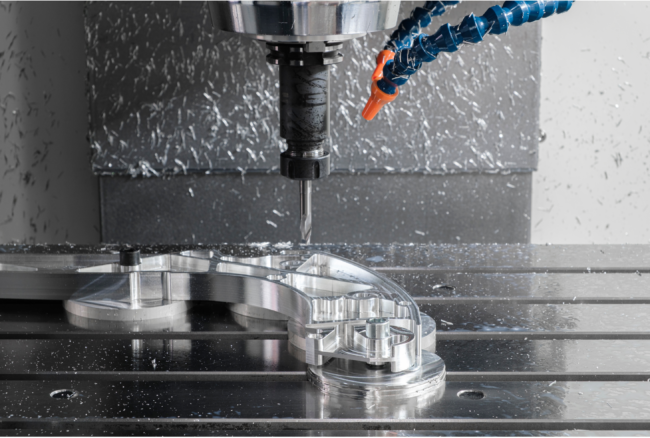
Precision machining serves as the backbone of die making and plays a pivotal role in the intricate and exacting process of creating dies for various industrial applications. In the realm of manufacturing, dies act as precision tools that mould, cut, or shape materials into specific forms, and the quality of these dies directly influences the accuracy and consistency of the final products. Precision machining techniques, including turning, milling, grinding, and advanced methods such as electrical discharge machining (EDM), are instrumental in shaping the components of dies with meticulous accuracy.
The role of precision machining in die making is multifaceted. It involves achieving tight tolerances, crafting complex geometries, refining surface finishes, and ensuring compatibility with a diverse range of materials. As industries demand increasingly sophisticated and precise components, the importance of precision machining in die making becomes even more pronounced. This synergy between precision machining and die making not only ensures the efficient mass production of components but also underpins the quality, durability, and versatility of dies across various manufacturing processes. This introduction sets the stage for an exploration of how precision machining techniques are intricately woven into the fabric of die making, influencing every aspect from design to performance.
Its crucial functions
Precision machining plays an essential and irreplaceable role in the art and science of die making. It provides the necessary tools and techniques to create highly accurate and complex dies that are the backbone of modern manufacturing. Here’s a breakdown of its crucial functions:
- Crafting precise geometries: Precision machining allows for the creation of dies with intricate and complex shapes, often featuring micro-features and tight tolerances. This is vital for producing high-quality parts with precise dimensions and finishes. Techniques like CNC machining, EDM (Electrical Discharge Machining), and laser machining enable the meticulous shaping of die cavities, cores, and other components with unwavering accuracy.
- Ensuring consistent performance: Precision machining guarantees the uniformity of die dimensions and features, leading to consistent and reliable production of identical parts. This is crucial for mass production processes, where even minor deviations can have significant consequences. Advanced machining technologies eliminate human error and ensure repeatable results batch after batch, enhancing the overall efficiency and quality of the manufacturing process.
- Enhancing die durability and lifespan: Through the use of high-quality materials and sophisticated machining techniques, dies can be made exceptionally strong and resistant to wear and tear. This prolongs their lifespan, reduces downtime for repairs and replacements, and ultimately leads to cost savings. Additionally, precision machining can create intricate cooling channels within the die, ensuring efficient heat dissipation and preventing thermal damage, further increasing its longevity.
- Expanding design possibilities: The capabilities of precision machining have expanded the horizons of die design, allowing for the creation of intricate and previously impossible geometries. This opens doors for innovative product development and the production of complex parts with advanced functionalities. The ability to precisely control surface finishes and textures further enhances the design possibilities, enabling the creation of dies that produce parts with specific aesthetic and performance characteristics.
- Optimising manufacturing processes: Precision machining can contribute to streamlining and optimising various manufacturing processes. By ensuring accurate and consistent die performance, it reduces scrap rates, eliminates rework, and optimises production times. Additionally, advanced machining techniques often enable the creation of dies that require fewer components or assembly steps, further simplifying the overall manufacturing process.
The advanced techniques that enable precision machining
Die making, the art of creating specialised tools for shaping materials, relies heavily on the precision machining arsenal. These advanced techniques enable the creation of highly accurate and complex dies, forming the backbone of modern manufacturing.
- CNC machining: CNC machining reigns supreme in die making, offering versatility and the ability to handle intricate geometries. Through computer control, CNC machines perform various operations like milling, turning, and grinding, bringing die designs to life with exceptional accuracy and repeatability.
- Electrical Discharge Machining (EDM): EDM utilises the power of electrical sparks to erode material. This unique approach tackles hardened materials and intricate shapes that would be challenging or impossible with conventional machining. In Wire EDM, a thin wire electrode acts as a scalpel, cutting intricate shapes and profiles with unparalleled accuracy whereas in Sinker EDM, a graphite electrode meticulously erodes material, creating cavities, punches, and other crucial die components.
- Laser machining: Laser machining wields a focused beam of light to melt and evaporate material, enabling the creation of precise cuts, grooves, and holes. This technique offers exceptional accuracy, minimal heat-affected zones, and the ability to machine a diverse range of materials.
- Micromachining: Micromachining techniques push the boundaries of precision, creating miniature dies and components with features on the order of micrometres. This unlocks possibilities for miniaturised parts and complex geometries across various industries like electronics, optics, and medical devices.
- Five-axis machining: Five-axis machining utilises advanced CNC machines with five axes of motion, enabling the simultaneous machining of complex geometries from multiple angles. This eliminates the need for multiple setups and reduces machining time, significantly increasing efficiency.
- Hybrid machining: Combining two or more machining techniques in a single process can unlock customised solutions tailored to specific die requirements. For instance, combining EDM with CNC machining can create complex features while maintaining high accuracy and surface finish.
Tooling and materials: The vital equation
The success of any precision machining operation, particularly in die making, hinges critically on the selection of the right tooling and materials. This intricate interplay between tools and workpiece materials dictates the outcome of the machining process, impacting factors like accuracy, efficiency, and surface finish.
- Choosing the right tool and material ensures:
- Optimal performance: Selecting the ideal tool and material combination ensures optimal performance, maximising efficiency, reducing machining time, and minimising tool wear.
- Desired results: The correct combination ensures the desired results are achieved, including the attainment of precise geometries, high-quality surface finishes, and dimensional accuracy.
- Cost efficiency: The right choices can lead to cost savings by minimising tool wear, optimising machining time, and reducing the need for rework or scrap.
- Increased productivity: Optimised tooling and materials contribute to increased productivity and efficiency by ensuring smooth operation and reducing downtime.
- Tool materials and their compatibility
- Carbide tools: These are versatile tools with high hardness, wear resistance, and durability, making them ideal for machining various materials, including steel, aluminium, and plastics.
- Diamond tools: These offer superior hardness and wear resistance, making them suitable for machining highly abrasive materials like ceramics and composites. However, they are more expensive than carbide tools.
- High-Speed Steel (HSS) tools: These are cost-effective options for general-purpose machining of softer materials like aluminium and brass. However, they are less wear-resistant than carbide tools and require more frequent sharpening.
- Ceramic tools: These are a newer category with excellent high-temperature properties and resistance to wear and tear. They are especially suitable for machining hardened steels and other challenging materials.
- What to keep in mind when selecting die materials?
- Application: The intended application of the die plays a crucial role. High-strength steels are typical for dies used in forming hard materials, while aluminium alloys are suitable for lower-stress applications.
- Desired properties: The desired properties of the die, such as wear resistance, corrosion resistance, and heat resistance, guide the material selection process.
- Machinability: The ease of machining the chosen material is important for efficient die production and minimising production costs.
- Some examples of material combinations are:
- HSS tools for machining aluminium dies: This is a cost-effective combination suitable for low-volume production of dies for forming soft materials.
- Carbide tools for machining steel dies: This combination offers a good balance of wear resistance and cost, making it suitable for medium to high-volume production of steel dies.
- Diamond tools for machining ceramic dies: This combination is essential for machining highly abrasive ceramic materials, even though it requires a higher initial investment.
Importance of quality control & inspection
In the realm of precision die making, where accuracy and functionality are paramount, quality control and inspection stand as the unwavering guardians. They ensure that dies meet stringent specifications, guaranteeing the production of high-quality parts and the longevity of the dies themselves.
- Quality control can ensure:
- Accuracy: Quality control ensures that dies are fabricated within the specified tolerances, guaranteeing the production of parts with consistent and precise dimensions.
- Functionality: It verifies that the dies operate as intended, ensuring smooth production and preventing defects in the final parts.
- Lifespan: By identifying potential issues early on, quality control helps prevent premature wear and tear, extending the lifespan of the dies and reducing maintenance costs.
- Cost effectiveness: Identifying and rectifying errors during the production process minimises scrap and rework, leading to cost savings and improved production efficiency.
- Improved die design and production: Quality control data provides valuable insights for improving die design and production processes, leading to continuous improvement and enhanced performance.
- Brand and reputation protection: By ensuring consistent quality in the production of parts, quality control protects the brand reputation and fosters customer trust.
- How to measure and inspect die features?
- Coordinate Measuring Machines (CMMs): These sophisticated instruments measure the dimensions and geometry of the die with high accuracy, providing detailed data on critical features.
- Optical comparators: These devices compare the die to a master image or drawing, visually highlighting any deviations or inconsistencies.
- Surface roughness testers: These instruments measure the surface finish of the die, ensuring it meets the required specifications for smooth operation and part quality.
- Hardness testers: They measure the hardness of the die material, ensuring it is strong enough to withstand the forces involved in the forming process.
- Ultrasonic testing: This non-destructive technique detects internal defects and cracks in the die material, ensuring its structural integrity.
Emerging trends
The landscape of precision machining is experiencing a wave of innovation, with several emerging trends poised to transform the future of die making. These advancements promise a future of increased design freedom, faster production times, improved die performance, enhanced quality control, and reduced costs, paving the way for innovation and growth in the die making industry.
Additive manufacturing, with its ability to create intricate geometries and conformal cooling channels, is reducing lead times and enabling weight optimisation.
Digital twin technology offers a virtual representation of dies for predictive maintenance, process optimisation, and virtual testing, leading to minimised downtime and improved performance.
Artificial intelligence and machine learning are optimising machining processes, predicting tool wear, and automating quality control, resulting in increased efficiency and reduced waste.
Ultra-precision machining techniques are pushing the boundaries of die complexity and surface finish, particularly relevant for micro dies.
Automation and robotics are enhancing safety, reducing labour costs, and increasing production volume, while collaborative robots are opening doors for safe and efficient human-robot interaction.
What lies ahead?
The future of precision die making is not only about technological advancement, it’s also about unlocking new opportunities and driving progress in various industries. From medical devices and aerospace to consumer electronics and automotive components, the ripple effect of these advancements will be felt throughout the global economy. As we look towards the future, we can expect precision die making to play a pivotal role in shaping the landscape of innovation, fostering economic growth, and ultimately, improving the quality of life for people around the world. This exciting journey promises to be one of continuous evolution, pushing the boundaries of what’s possible and shaping the future of manufacturing across diverse industries.
COMMENTS