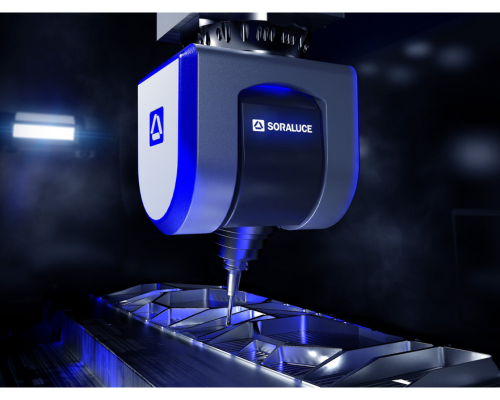
Soraluce introduces a new generation of milling machines that are more powerful, precise, and intelligent than ever before. These machines are designed to meet the evolving demands of industries such as aerospace, energy, and mold & die, while also preparing for a future defined by automation, connectivity, and data intelligence.
At Soraluce, innovation isn’t a destination—it’s the path forward. We drive the future of machining by developing solutions that foresee industry trends, resolve real-world production challenges, and help our customers maintain their competitive edge. Every project represents a chance to explore new frontiers together, blending our technological expertise with our clients’ pursuit of excellence.
What truly defines Soraluce’s philosophy, however, extends beyond technology—it’s rooted in trust. The company partners closely with customers to tailor solutions around specific processes, challenges, and long-term goals. Through each collaboration, Soraluce delivers more than just machines—it delivers genuine commitment.
New Dynamic Line High-Rail Gantry Machines
Soraluce’s new High-Rail Gantry Machines are designed to elevate manufacturing to new heights of performance. With high-speed cutting capabilities, exceptional precision, and the capacity for heavy-duty machining, these machines combine the company’s deep milling expertise with cutting-edge technology.
The Dynamic Line includes three machine models tailored for sectors like aerospace, mold & die, and mechanical engineering, with configurations optimized for composites, light alloys, and steel-based materials.
Engineered to meet the specific needs of various industries and applications, the machines can be equipped with either 5-axis contouring fork-type or high-torque milling heads—ideal for machining complex geometries. A state-of-the-art splash guarding system ensures a clean, safe environment, while integrated dust extraction—both inside the enclosure and directly at the heads—efficiently removes debris, maintaining performance and cleanliness.
Delivering top-tier dynamics, these machines offer axis speeds of up to 60,000 mm/min and acceleration of 4 m/s². Their innovative 5-axis heads reach spindle speeds up to 30,000 rpm, enabling fast and precise contouring.
Precision is reinforced through thermal stability systems, calibrated kinematics, and advanced high-speed finishing technologies that ensure exceptional surface quality without sacrificing accuracy.
With powerful milling heads offering up to 73 kW and 2,000 Nm of torque, and intelligent damping systems like DAS+ and DWS improving structural integrity, the Dynamic Line guarantees high-performance, reliable machining even in the most demanding scenarios.
World Premiere of the Soraluce Fork-Type Head
Taking center stage at EMO is the world premiere of Soraluce’s latest breakthrough in 5-axis machining: the new Fork-Type Head—a next-generation innovation that redefines flexibility, precision, and stability.
Engineered to deliver exceptional accuracy and adaptability for complex geometries, this cutting-edge head is designed to integrate perfectly with the new Dynamic Line of High-Rail Gantry Machines. Tailored for the demanding requirements of the aerospace and mold & die sectors, it enables precise, stable, and highly efficient machining of intricate contours and hard-to-access surfaces.
The Fork-Type Head features a true 5-axis configuration powered by direct-drive torque motors, ensuring smooth, backlash-free movement and rapid response. Its fully water-cooled design guarantees optimal thermal stability, while high-precision optical encoders provide accurate angular feedback for consistent performance, even during long, high-speed operations. With a power rating of up to 100 kW and spindle speeds reaching 30,000 rpm, the head is capable of both heavy-duty and high-speed machining. Optional high-frequency electrospindles are available to tailor the setup for specific materials and cutting conditions.
Built for superior mechanical performance and full thermal stability, the new Fork-Type Head enhances machining versatility—empowering manufacturers to take on increasingly complex components and challenging materials with confidence.
Upgraded Soraluce FP-Series
Soraluce proudly introduces the upgraded version of its flagship FP floor-type milling-boring machine—now offering increased capacity, higher speeds, enhanced power, and unmatched precision. These improvements are designed to optimize machine performance while expanding customization possibilities to meet the unique requirements of each customer.
The FP series is a productivity powerhouse that combines high cutting capacity with exceptional flexibility. Engineered to meet the most demanding production needs, the FP delivers top-tier efficiency, quality, and accuracy, making it the go-to solution for specialized and highly competitive machining environments.
Thanks to its adaptable machine architecture, the FP supports multiple configurations, enabling the use of several workstations and pendulum machining—significantly reducing non-productive time.
Key specifications include a generous longitudinal traverse of 8,000 mm, vertical traverse of 3,200 mm, and an upgraded cross traverse of 1,800 mm. The machine is powered by direct-drive motors with high torque integrated into the ram, supported by an advanced cooling system to ensure optimal reliability and precision. A standout feature is the powerful 60 kW Soraluce motorization operating at 7,000 rpm. The machine is equipped with a universal stepless head, ideal for high-precision interpolation machining.
Integrated into the vertical saddle is the Ram Balance system—a closed-loop solution that continuously monitors and corrects the ram’s geometrical accuracy, straightness, and parallelism during both vertical and cross-axis movement. Operating as a dedicated CNC axis with its own direct position measurement, this system significantly enhances overall precision—especially when combined with the automatic head changing system.
The automatic head changer enables effortless transitions between multiple setups. The CNC compensates for the weight differences among various heads, maintaining consistent machining accuracy across all configurations.
With these advancements, the upgraded Soraluce FP-series sets a new industry benchmark in milling and boring technology—delivering peak performance, enhanced flexibility, and precise results for even the most demanding industrial applications.
Shaping Aerospace Progress
Enhance efficiency, precision, and reliability in aerospace component machining with Soraluce’s cutting-edge technologies—spanning 5-axis machining, multitasking, automation, vibration control, and intelligent digital monitoring. These solutions are developed to meet the stringent requirements of critical aerospace components including engines, structural assemblies, fuselages, and landing gear.
Soraluce’s systems are built to machine the industry’s most challenging materials—such as high-strength titanium alloys, Inconel, large aluminum structures, and advanced composites—while ensuring dimensional precision, superior surface quality, and stable processes. From complex aerostructures to essential engine parts, Soraluce consistently delivers high-quality, dependable results.
Central to the offering is 5-axis machining, which facilitates the production of complex geometries in a single setup, significantly reducing cycle times while preserving the highest levels of accuracy. This flexibility empowers manufacturers to respond swiftly to varying materials and evolving industry demands.
To overcome one of the toughest challenges in machining advanced materials—vibration—Soraluce incorporates active damping systems like DAS+ (Dynamic Active Stabilizer), which detect and mitigate vibrations in real time. This ensures smoother, safer, and more precise machining, while also prolonging tool life and enhancing surface finish.
The multitasking capability combines milling, turning, drilling, grinding, riveting, and friction welding within a single setup—reducing part handling and setup time, and ultimately minimizing errors and overall production costs.
Automation drives further gains in efficiency, ranging from standalone machines equipped with CNC pallet control to advanced, flexible machining cells managed by proprietary software. This leads to optimized workflows, increased throughput, and enhanced production adaptability.
Adding to this is intelligent monitoring technology that offers real-time visibility into machining processes to boost productivity and reduce equipment wear. It monitors production, ensures traceability, logs downtime, manages tool wear, and seamlessly integrates with ERP and OEE systems, supporting large-scale manufacturing operations.
Collectively, these technologies form a complete aerospace machining solution—delivering superior performance, lower operational costs, and end-to-end process control from the first component to full-scale production. Soraluce also provides turnkey solutions tailored to customer requirements, including specialized heads, custom tooling, and validated machining processes to ensure optimal reliability and productivity from day one.
Smart Automation
In response to the increasing demand for efficient and flexible production in complex, multi-reference environments, Soraluce introduces its Smart Automated Solutions—engineered to enhance productivity and minimize non-productive time throughout the entire manufacturing chain.
This level of automation surpasses conventional offerings. Soraluce’s systems are designed to handle large-scale components, with tailored configurations that adapt seamlessly to various part types and batch sizes. Whether it’s a single machine featuring CNC-integrated pallet control or an advanced flexible cell managed via industrial PCs, every solution is purpose-built for efficiency and real-world performance.
A key highlight is the company’s palletizing systems, which are developed with a focus on precision, modularity, and adaptability. These solutions streamline workflow, shorten changeover times, and significantly elevate overall plant efficiency.
To further increase manufacturing agility, Soraluce has incorporated centralized tool storage systems that are fully integrated with its proprietary tool management software. This interlinked architecture allows tools to be shared between machines, avoids selection errors, reduces duplicate tooling needs, and minimizes the space required for tool storage. All tool automation is data-driven—guided by live production orders, delivery timelines, and tool availability—ensuring just-in-time operations.
At the heart of this automation ecosystem is the Control System, a robust software platform developed internally by Soraluce Software Factory. Built around the innovative Job List concept, it enables full integration of every element in the manufacturing flow: machines, parts, pallets, tools, CNC programs, fixtures, and operations. This unified platform coordinates the entire cell, delivering maximum productivity along with complete traceability, process clarity, and seamless functionality at every stage of the production process.
COMMENTS