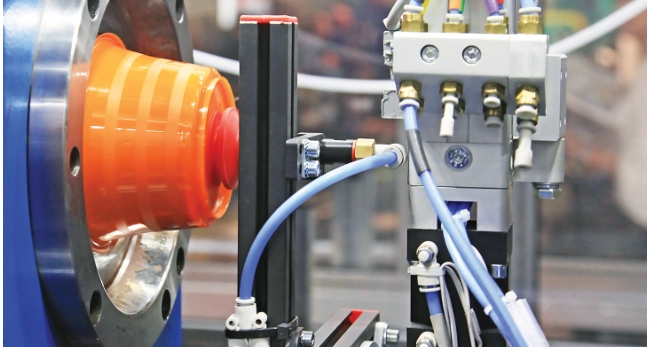
– Vivek Singh
The increased demand for FMCGs has made blow moulding one of the most go-to manufacturing processes. By combining speed, robustness, and efficiency, blow moulding can create strong, lightweight products with precise shapes, making it ideal for packaging, automotive, and medical industries. This article explores how the top three key drivers in blow moulding, namely, central chilling systems, multi-layer and multi-material capabilities, and high-speed production systems, can help you optimise precision, and enhance performance and manufacturing efficiency.
Blow moulding is transforming the way we make the products that we use every day. From simple bottles and containers to complex parts like fuel tanks, automotive ducts, and even medical devices, this process makes it possible to create durable, lightweight, and affordable items at scale. As industries push for smarter, faster and more sustainable manufacturing, blow moulding has stepped up—becoming not just a 22 method of production, but a driver of innovation.
Blow Moulding: An Overview
Blow moulding is an industrial manufacturing process that’s used to create hollow plastic parts. In this process, a parison, which is a molten plastic tube, is formed and then inflated into a mould cavity to take on its shape. This method is pivotal in mass-producing items with uniform shapes and sizes, as it ensures efficiency and scalability.
Types of Blow Moulding Processes
Blow moulding includes a number of processes designed to fulfill specific manufacturing requirements, all of which rely on the core principle of producing hollow plastic parts. The three main types are Extrusion Blow Moulding (EBM), which involves extruding and inflating a parison within a mould; Injection Blow Moulding (IBM), which involves injecting a preform and blowing it into shape; and Stretch Blow Moulding (SBM), which stretches and inflates the parison to increase strength and clarity. Each process has distinct advantages and applications, making them essential for producing a wide range of plastic items across several industries. (See Table 1) Understanding these categories is critical for businesses looking to improve their manufacturing processes and meet a wide range of consumer needs.
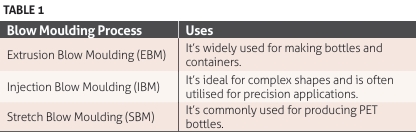
Industries and Applications
Blow moulding is a highly adaptable manufacturing process that is commonly used in a variety of sectors, most notably for the production of hollow plastic goods. The packaging sector mainly relies on blow moulding to produce bottles, containers, and drums. These items are crucial in industries like food and beverage, medical, and personal care, where durability, lightweight design, and affordability are critical.
The automotive sector also uses blow moulding to make interior and exterior components such as fuel tanks, air ducts, and bumpers. This technology enables manufacturers to produce complicated, lightweight parts with precise dimensional control, resulting in increased vehicle performance and fuel efficiency.
In the medical industry, blow moulding is used to manufacture sterile containers, vials, and medical gadgets that exceed demanding safety and precision standards. The adaptability of blow moulding enables customisation in both shape and size, which is critical for the wide range of medical applications.
Furthermore, the consumer products industry opts for blow moulding to manufacture toys, athletic goods, and household items. Blow moulding’s versatility to material kinds and product designs makes it a popular choice in this industry.
In each of these industries, blow moulding’s key advantages—low cost, high production speed, and capacity to produce precise shapes— make it an essential manufacturing technique, satisfying the criteria for mass production, uniformity, and quality control.
The 3 Key Drivers of Blow Moulding
Advancements in cooling, material innovation, and production speed can influence the efficiency and quality of blow moulding. Let’s review how key drivers such as central chilling systems, multi-layer and multi-material capabilities, and high-speed production systems optimise precision, performance, and manufacturing efficiency:
Central Chilling Systems: Precision and Energy Efficiency In the blow moulding process, maintaining stable temperatures is essential. Central chilling systems have proven to be a game-changer here; they offer precise temperature control, thereby improving product quality and reducing material defects. These systems optimise cooling efficiency across numerous machines, resulting in significant energy savings. For mould makers, building tools that are compatible with temperature sensitive materials becomes critical, allowing them to cater to high-performance applications. The central chilling systems are a boon for them, as these can be customised. For example, cooling systems can be tailored to handle specific mould sizes, accommodate multiple machines, or manage different cooling requirements for diverse materials.
Multi-Layer and Multi-Material Capabilities: Advancing Precision and Performance With an increasing need for high performance packaging solutions, notably in the food and beverage industries, blow moulding machines are evolving to handle multi-layer and multi-material production in a single cycle. These machines use co-extrusion technology, which offers precise control over material distribution, resulting in homogenous layers with barrier qualities, strength, and endurance. Mould manufacturers play a key role in this transition, creating specialised dies and moulds that allow for seamless material flow and integration. The challenge lies in optimising mould cooling and ensuring proper material adhesion, as different polymers require different processing conditions. High-performance applications such as pharmaceutical and industrial grade containers necessitate careful control over material parameters such as thickness, viscosity and temperature during moulding. Mould durability and wear resistance become crucial variables, particularly when working with novel, frequently abrasive materials.
High-Speed Production Systems: Optimal Efficiency In modern blow moulding, the focus is on ensuring the quality of the end product while increasing throughput by speeding up cycle time. To satisfy these expectations, machines are now designed to operate at higher rates, necessitating precision tools that can resist increased stress during quick operations. Mould makers must build moulds that can withstand the physical pressures of rapid manufacturing while also maintaining dimensional accuracy and surface polish throughout shorter cycles. To achieve this, specialised cooling systems are required to prevent overheating and distortion of the moulded components. The cooling systems must be appropriately calibrated to regulate the heat created during high-speed moulding while maintaining cycle time and product quality.
Centralised Cooling Systems and Conformal Cooling
Along with centralised cooling systems, another similar trend for temperature management in blow moulding is conformal cooling. The growing need for tools to withstand new sustainable materials such as PLA and PHA can be satisfied by creating new mould designs and coatings that can handle higher temperatures and moisture sensitivity, resulting in longer mould life and better product quality. Centralised cooling systems and conformal cooling are essential for managing heat cycles, especially when processing advanced materials such as bio-based polymers, which exhibit unique thermal behaviours.
Advantages for Toolmakers
Blow moulding has various technological advantages for toolmakers, particularly in high-volume production. For toolmakers, these advantages, together with blow moulding’s speed and material efficiency, make it an essential production method, particularly in industries such as packaging, automotive, and medical devices:
The technology allows for the rapid manufacturing of huge quantities of identical moulds, lowering manufacturing expenses and increasing overall efficiency.
It excels in producing complex shapes with thin walls and hollow interiors—features that would be difficult or costly to achieve using other methods like injection moulding.
In addition, blow moulding produces minimal material waste because extra plastic can be efficiently recovered and reused, making it a sustainable solution.
Another key advantage is the capacity to combine several materials into a single product, which is suitable for creating multi layered containers with varying qualities. This adaptability improves product performance in areas such as barrier protection and durability.
Blow moulding also provides design diversity, allowing for the fabrication of both small consumer goods and huge industrial components.
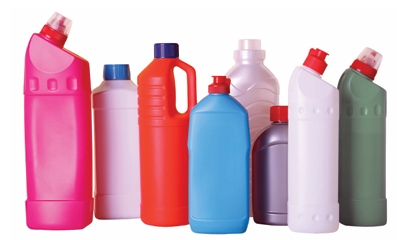
Conclusion
The growing demand for consumer goods is intensifying the need for faster manufacturing of moulds and tools. The rise in demand for more sophisticated goods will result in a rise in multi-layered, multi-material goods. This trend, however, brings significant challenges to mould durability, including heat instability, moisture sensitivity, and accelerated wear. To overcome these issues, mould manufacturers—especially SMEs and MSMEs in India—must adopt innovative solutions such as advanced centralised cooling systems, heat-resistant materials, and optimised mould designs to enhance performance and extend tool life.
Additionally, with sustainability gaining prominence, innovation in mould technology becomes critical for mould makers looking to gain a competitive edge and remain relevant. This includes adjusting to new polymers and materials that need greater durability and performance.
Besides, by utilising trends such as sophisticated cooling systems, multi-material moulding capabilities, and high-speed production technologies, Indian mould makers can not only tackle rising obstacles but also enhance production efficiency, minimise downtime, and reduce maintenance costs. Adopting these innovations will help them boost their position in the global market, ensuring that they are well prepared to cater to the future needs and meet the industry standards.
Images used for representation only. Courtesy Envato Elements
This article was published in TAGMA Times
COMMENTS