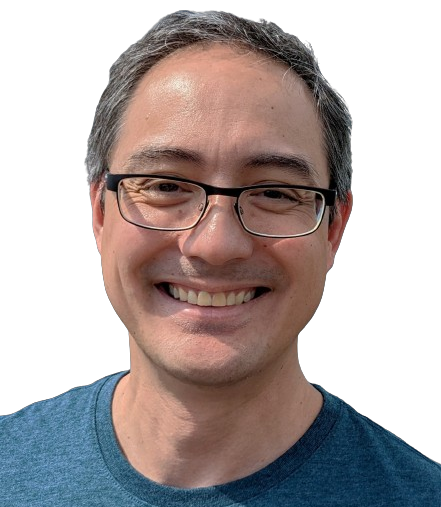
Nishant Kashyap, Editor of ToolingTales, recently had an insightful conversation with Paul J. Gray, Vice President – R&D and Product Development at HURCO. Their discussion delved into the major trends shaping the CNC industry, including automation, digital twin technology, intelligent manufacturing, and substantial investments in research and development (R&D). Paul shed light on HURCO’s innovative strides, particularly their emphasis on automation solutions, solid model import software, and collaboration with Universal Robots for cost-effective CNC machine automation.
You recently showcased many technologies at the recently concluded EMO 2023. Can you provide an overview of Hurco’s presence and participation at EMO Hannover 2023? What were the key highlights or products you are showcasing?
At this edition of EMO, we have taken the automation to the next level. We showcased 2 ProCobots; Hurco’s own plug-and-play collaborative robot solution, feeding both a lathe and a vertical machining centre. With Hurco ProCobot software one can reduce programming time to a minimum, thereby making automation of small batches a possibility. The collaborative robots (cobots) from ProCobots, combined with Hurco technology, ensure the cobots are easy to set up and easy to program. With ProCobots, one operator can run three or four machines at once.
For this, we partnered with Universal Robots (UR) to create practical CNC machine automation solutions that are affordable, practical, flexible, compact, and eliminate the need to call an expensive integrator each time you want to change your automation or move the system to different machines.
Another standout feature at our booth was the Solid Model Import software. This groundbreaking technology allows direct programming from an STP file at the machine control, eliminating the necessity for CADCAM. For instance, on five-axis machines requiring cuts at various angles, holes, pockets, or even with islands, simply selecting the STP file prompts the control system to automatically generate the toolpath.
Apart from this there are many other technologies but these two are the highlight of our booth.
What are some of the key technological trends or breakthroughs in CNC machining that have emerged in recent years?
There are quite a few trends emerging but I would like to highlight the four most important ones.
- Automation: Emerging as a pivotal trend in the CNC industry, automation addresses the challenge of skilled manpower shortages while enhancing efficiency, speed, and machining quality. This transformative technology mitigates human errors, minimizes waste and downtime, and elevates the safety and productivity of CNC machines. Utilizing diverse technologies, including robotics, cobots, software, and sensors, automation offers comprehensive solutions. For instance, robotics handles workpiece loading and unloading, cobots collaborate with human operators, software optimizes machining parameters, and sensors monitor machine conditions and performance.
- Digital Twin: Digital twin stands out as a significant trend in the CNC industry, offering a virtual representation of the physical CNC machine and its surroundings. This technology facilitates pre-production simulation, analysis, and optimization of the machining process. Moreover, digital twin aids in real-time maintenance, troubleshooting, and enhancements by providing valuable data and feedback. It also fosters seamless collaboration among CNC machine operators, engineers, and managers.
- Intelligent Manufacturing: The ongoing trend of intelligent manufacturing seeks to integrate information technology, communication technology, and automation to establish a smart and interconnected CNC machining system. This approach addresses the evolving customer demands for customization, quality, and timely delivery. Moreover, intelligent manufacturing enables the CNC industry to adapt to dynamic market and environmental conditions, including competition, regulations, and sustainability. Achieving intelligent manufacturing involves leveraging technologies such as artificial intelligence, machine learning, big data, cloud computing, and the Internet of Things.
- Investment in R&D: The commitment to investment in research and development underscores the CNC industry’s continuous pursuit of innovation and advancement. Fueled by escalating customer expectations for enhanced efficiency and productivity, CNC manufacturers worldwide must persistently innovate to meet growing demands. At Hurco, our primary focus is on R&D, and we invest significant efforts in this crucial area.
In your opinion, what are the current challenges and opportunities in the CNC machining industry, and how is Hurco positioned to address them?
The challenges and opportunities for the CNC industry after COVID are closely related to the trend of automation. Automation can help the CNC industry overcome the problems caused by the disruption of the supply chain, the shortage of skilled manpower, and the changing customer demands. Automation can also help the CNC industry improve the efficiency, quality, and flexibility of the machining process. Automation can be achieved by using various technologies, such as robotics, software, sensors, artificial intelligence, and cloud computing.
The opportunities for the CNC industry after COVID are also influenced by the recovery and growth of the global market, especially in the US and India. These markets have a high demand for CNC machines and services, especially for the healthcare, aerospace, and defense sectors. The CNC industry can leverage these opportunities by offering innovative and customized solutions, such as digital twin, intelligent manufacturing, and remote diagnostics. The CNC industry can also benefit from the increased investment in R&D, which can help create new and improved products, services, and processes.
What advice or tips can you offer to manufacturers looking to choose the right CNC machine for their specific applications and industries?
There are numerous options available when it comes to choosing a CNC machine, each with its own set of features and capabilities. While budget considerations are crucial, the key lies in collaborating with representatives from machine tool companies. Engaging with sales representatives and distributors allows for a tailored approach to finding the most suitable solution for your specific needs.
For instance, our division in Hurco, India, works closely with clients to offer CNC machines that align with operator requirements. This involves understanding factors like ease of programming and familiarity with specific controls, such as the widely used Fanuc control on Takumi systems.
Maintaining continuity in your shop’s operations is vital. If your operators are accustomed to a particular control system, like Fanuc, it makes sense to stick with it. In the context of die and mould manufacturing, serious consideration should be given to five-axis machining. Even if a company feels it may not be fully ready for it, modern solutions, like Hurco’s simplified five-axis system, streamline the process by automatically programming angles.
Companies exploring new CNC machines should assess their setups and operations, giving due consideration to five-axis capabilities. The advantages, including enhanced part accuracy, fixture reliability, and the efficiency gained from machining multiple sides in a single setup, often outweigh the complexities associated with traditional three-axis machines and multiple fixtures.
Can you provide insights into Hurco’s research and development efforts and any upcoming innovations or projects that the company is excited about?
Engaging in research and development is an exciting aspect of our work, where we constantly strive to push boundaries. We have initiated a research program in collaboration with the University of Waterloo in Ontario, Canada, focusing on leveraging artificial intelligence (AI) in intelligent ways with CNC machines.
Over the past few years, our research has delved into areas such as anomaly detection for chatter suppression, feature recognition, and analyzing work volume using camera systems. Our vision is straightforward: with the simplest control on the market, we are committed to making operators’ and programmers’ lives easier. Any step that contributes to this goal is a step we’re eager to take.
Incorporating AI solutions to enhance the autonomy of CNC machines is a key focus. Through ongoing research, we aim to develop practical solutions that empower our customers to benefit from advancements in technology.
What are your views on the Indian market?
The Indian market presents a tremendous opportunity for everyone, extending beyond just Hurco and our division. Hurco India has made remarkable progress in establishing our name brand, strengthening our service and sales organizations, and effectively communicating the opportunities inherent in our products and controls. Additionally, the Takumi brand, positioned as a sister brand, complements what we can offer to the Indian market. We are genuinely excited about the unfolding prospects in India. For any business looking ahead, considering India is imperative.
COMMENTS