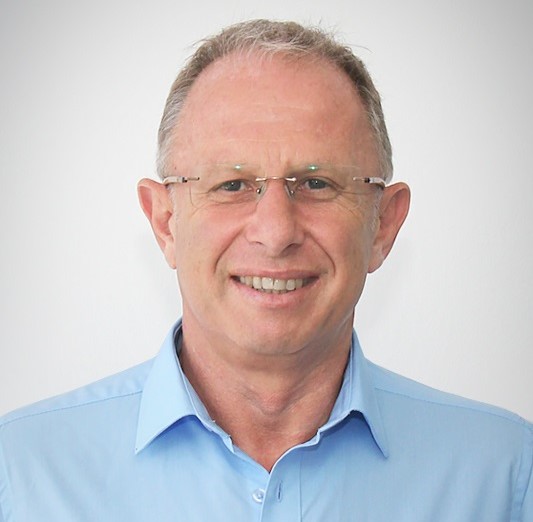
In an interview with Baruch Books, Vice President – Sales and Marketing at Vargus Ltd, and Rahul Patil, Managing Director of Vargus India, conducted by Nishant Kashyap, Editor of Toolingtales.com, the discussion delves into the key features of the Vargus booth, the groundbreaking MACH line of products, current trends in the cutting tool industry, and their strategic plans for the Indian market during EMO 2023.
Please tell us the highlight of your booth? What are you showcasing at this edition of EMO 2023?
EMO holds significant importance for us as it serves as a platform to unveil our latest and innovative solutions. Renowned as a world leader in threading, grooving, turning, and deburring tools for metalworking and plastics industries, we’ve gained specific recognition for our threading tools, catering to companies of all sizes worldwide.
At EMO 2023, our spotlight is on the recently launched MACH line of supersonic threading tools – the MACH TT for turning applications and MACH TM for milling applications.
The game-changing MACH TT boasts multiple advancements, distinguishing it from competitors. It reduces the number of passes and machining time by 60%, while increasing tool life by 50%. Designed for high loads, it offers high rigidity and delivers a smooth finish.
Our latest addition to the thread milling range, the MACH TM, stands out as the best thread milling tool by industry standards. With up to a 60% reduction in machining time, a 25% increase in tool life, and excellent surface finish, it has garnered attention in the market since its launch a year and a half ago.
While introducing new innovations requires time and education, I am confident that in the next five years, threads in the market will operate akin to the efficiency of the MACH line.
That’s remarkable benefit. Do you have any case study to share with us to understand more about this tool helped the customer?
Before delving into your question, it’s crucial to highlight our robust research and development team and facilities. Our extensive R&D capabilities allow us to develop and test products thoroughly. Any product we introduce to the market undergoes rigorous in-house testing for an extended period to comprehensively understand its performance. Additionally, upon launch, we provide recommendations on optimal tool usage to maximize effectiveness.
The MACH Line, launched approximately 1.5 years ago, has been distributed to numerous customers globally. We collected data from 350 customers across diverse applications in various countries. Remarkably, almost 98% of customers achieved the anticipated results. The remaining 2% who didn’t attain the desired outcome did not follow our recommendations.
As a breakthrough product, MACH Line introduces new methods and techniques. It’s crucial for customers to adhere to our recommendations. We also have application experts in each country available to assist customers with any technical issues they may encounter.
Our testing of the MACH Line covered a wide range of applications and materials, including Inkonal and titanium at high temperatures, with successful outcomes.
In essence, when we discuss the benefits we aim to provide, our commitment is to empower customers with the best possible results.
The cutting tool technology has evolved a lot in recent time. According to you what are the growing trends in the cutting tool technology?
There are many trends that we feel are going to shape the industry:
Material Science Advancements:
- High-Performance Materials: The continuous evolution and introduction of high-performance materials, such as advanced alloys, composites, and superalloys, are driving innovations in cutting tools. These materials demand cutting tools with enhanced hardness, wear resistance, and toughness to maintain efficiency during machining processes.
- Coating Technologies: The emphasis on material science extends to the development of advanced coating technologies. Cutting tools with coatings like titanium nitride (TiN), titanium carbonitride (TiCN), and diamond-like carbon (DLC) coatings enhance tool life, reduce friction, and improve overall performance.
New Geometries for Enhanced Performance:
- Multi-Axis Machining: With the rise of complex and intricate part designs, cutting tools are evolving with new geometries to facilitate multi-axis machining. This enables manufacturers to achieve precise and intricate cuts, enhancing the overall efficiency and accuracy of machining operations.
- Optimized Chip Formation: Innovations in tool geometry focus on optimizing chip formation. Enhanced chip control not only improves surface finish but also contributes to better heat dissipation, extending tool life and minimizing tool wear.
Diverse Applications and Industry-Specific Solutions:
- Customization for Specific Industries: The cutting tool industry is witnessing a trend towards customization to meet the unique demands of various industries. Tailoring cutting tools for specific applications in aerospace, automotive, medical, and energy sectors ensures optimal performance in diverse machining environments.
- Versatility for Multi-Material Machining: As industries increasingly adopt multi-material designs, cutting tools are adapting to handle a wide range of materials in a single machining operation. This versatility is essential for addressing the demands of modern manufacturing processes.
Digitization and Smart Technologies:
- IoT Integration: The cutting tool industry is embracing digitization through the integration of Internet of Things (IoT) technologies. Smart cutting tools equipped with sensors provide real-time data on tool conditions, enabling predictive maintenance, reducing downtime, and optimizing tool life.
In summary, the cutting tool industry is experiencing a transformative phase driven by advancements in material science, innovative tool geometries, a focus on diverse applications, and the integration of digitization and smart technologies. These trends collectively contribute to more efficient and precise machining processes across various industries.
Automotive industry has always been the biggest consumer of cutting tools. What are the other emerging sectors that are going to generate good business for cutting tool industry in coming years?
Several industries are poised to generate substantial demand for the cutting tool sector in the near future. Primarily, the medical industry stands out. The continuous advancements in medical engineering have significantly expanded opportunities for the cutting tool industry. While it has been a staple, we anticipate a surge in demand within the medical sector.
Aerospace, encompassing both civilian and defense aircraft, represents another robust industry. India’s record-breaking order last year, coupled with a global trend, indicates a sustained demand for cutting tools in this sector.
Additionally, the defense industry is expected to contribute significantly to the growing demand for cutting tools. The multifaceted requirements within the defense sector are likely to fuel substantial growth in the cutting tool industry.

Rahul Patil
What about India? Which industry is growing in India?
Rahul: In India, we are witnessing a significant demand from the medical and aerospace industries. The unique nature of these sectors, requiring high precision, aligns perfectly with the capabilities of our tools.
Another major industry in India is electronics. We have tailored products and strategies to cater to this sector. Currently collaborating with some of the largest electronics companies, we aim to replicate and expand our success in India.
Our plans for the Indian market are extensive, and we will implement them systematically as opportunities arise.
And how the customer expectations are evolving in India?
Rahul: As the Indian industrial sector undergoes rapid growth and technological advancements, there is a heightened demand for cutting-edge cutting tools. This surge is driven by escalating expectations in quality, increased investments, and a focus on high-end tools. Indian customers now prioritize faster lead times, emphasizing the need for efficient production cycles. Additionally, after-sales support has emerged as a crucial factor, with customers seeking comprehensive assistance. Our company is well-positioned to meet these evolving demands, offering not only high-quality cutting tools but also efficient after-sales support to ensure a seamless experience for our customers.
As we all know the Indian manufacturing industry is growing rapidly. What are your plans for the Indian market?
At Vargus, we deeply value the Indian market and are dedicated to serving the country with our innovative products. The prevailing sentiment in India is notably positive, with many large manufacturing companies establishing production facilities in the country. Recognizing the resulting surge in demand for machine tools, we are keen on capturing this opportunity.
Having a longstanding presence in the Indian market, we are contemplating the initiation of a small-scale production unit to meet domestic demand. Following a thorough assessment of conditions, our plan includes continued expansion to further contribute to India’s industrial growth.
COMMENTS