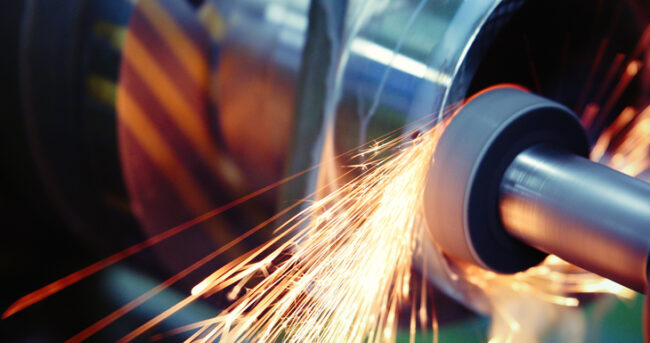
Source: Envato
The tooling industry is rapidly gaining prominence on the global stage due to its pivotal role in advancing manufacturing processes. With a surge in demand for precision tools, moulds, dies, jigs and fixtures across various sectors, the tooling industry is witnessing increased recognition for its crucial contributions to innovation, efficiency, and quality in production. How could your tooling company reap the rewards of this increasing demand? The ‘Indian Tool Room Industry Analysis, August 2023’ that’s been jointly compiled by TAGMA India and Nomura Research Institute, Ltd., has the answer.
The global tooling industry and the Indian tooling industry have been growing steadily post the pandemic. While the global tool room industry stood at USD 80 billion in 2021 post COVID-19, the total market size of the tool room industry in India is estimated to be ~INR 23,600 crore. Interestingly, ~34% of the tooling demand is met through imports with ~80% of the imports from China, South Korea, Japan, and Taiwan. ~15% of tooling production in India is exported – USA, Spain, Mexico, and Germany are major export destinations. The share of Commercial Tool Rooms (CTRs) in total demand grew at ~8.1% & Captive Tool Rooms grew at ~1.5%, while imports have been almost stagnant with minor changes.
The abovementioned interesting findings were revealed in the ‘Indian Tool Room Industry Analysis, August 2023’ that was released at the recently held International Tooling Summit. The report has been jointly compiled by the Tool and Gauge Manufacturers Association (TAGMA) India and Nomura Research Institute, Ltd.
Indian tool room industry
With the demand side of moulds estimated at ~INR 21,900 crore and the demand for jigs, fixtures & gauges estimated at ~INR 1,700 crore, the total market size of the tool room industry in India is estimated to be ~INR 23,600 crore.
Imports and Exports
According to the report, the tooling imports into India are ~4x the tooling exports from India in terms of value with China and Korea being the major exporters.
The total tooling imports are estimated at ~INR 8,000 crore. Of this estimate, Sheet Metal Dies comprise ~INR 2,100 crore (i.e. 26%), Plastic Moulds comprise INR 3,000 crore (i.e. 38%), while Die Casting Dies and Jigs, Fixtures & Gauges comprise ~INR 2,000 crore (i.e. 25%) and ~ INR 900 crore (i.e. 11%), respectively. The major import sources are China at 38%, Korea at 35%, Japan at 9%, and Taiwan at 3%.
The total tooling exports are estimated at ~INR 1900 crore. Of this estimate, Sheet Metal Dies comprise ~INR 350 crore (i.e. 18%), Plastic Moulds comprise ~INR 700 crore (i.e. 37%), while Die Casting Dies comprise ~ INR 550 crore (i.e. 29%) and Jigs, Fixtures & Gauges comprise ~INR 300 crore (i.e. 16%). The report cites the major export destinations as USA at 17%, both Spain and Mexico at 5% each, and Germany at 4%.
Demand trends
CTR share grew at ~8.1%, while imports and captive tool rooms have been almost stagnant with minor change.
Commercial tool rooms have a higher growth rate than captive tool rooms. The report states the major reason for this is the capex considerations for the OEMs and Tier-1 suppliers for capacity enhancement. Indian tool rooms have slowly been catching up to meet the requirements of Indian customers, which is reflected in the high growth and marginally reduced imports. The push for localisation by the Indian OEMs have also helped here.
In the automotive sector, EV start-ups are largely looking at one-stop solutions for their tooling requirements. Hence, they rely on imports as a blueprint solution, as they prefer one-stop solution for the components.
The automotive sector continues to be the largest end-user of tooling in India, with auto OEMs and Tier-1s together accounting for more than 60% of tooling demand India
The aerospace & defence sector has grown with its current market share of ~1% from an insignificant share in FY 2019 to FY 2023 due to the government’s push towards localisation of aerospace & defence equipment.
Plastic moulds continues to be the largest segment; die casting dies grew at slower rate of ~1.1%.

Source: NRI Analysis
Technology trends: Tooling Demand Side
As the shift to EV gains traction, the demand for plastic moulds, and aluminium forging could replace conventional demand. Also, the demand for lightweight materials is increasing in industries such as automotive, and new sectors like aviation. Besides, an increase in facelifts and new designs with new technologies at the end of the product lifecycle is likely to create demand for tooling. And, demand from developing sectors is on the rise with the Government of India’s push to localise production through initiatives like ‘Make in India’, states the report.
Technology trends: Tooling Supply Side
According to the report, newer production processes like 3D printing, and additive manufacturing, have the potential to drive supply in future, while the durability provided by composite materials could make ITRs more efficient, increasing capabilities and supply.
Government initiatives
The Government of India has undertaken various initiatives to offer a boost to the Indian tooling industry, states the report while highlighting the following:
- In 2014, MHI launched Phase I of ‘Enhancement of Competitiveness in Capital Goods Sector’ with a budget of ~INR 580 crore.
- In 2022,Phase II of ‘Enhancement of Competitiveness in Capital Goods Sector’ was launched with an allocation of INR ~1200 crore.
- The scheme was successful in the tooling industry with development of new prototypes, centres & platforms
- The Ministry of Commerce and Industry is encouraging the export of capital goods through tax concessions & incentives
- The Ministry of MSME has reimbursement schemes to encourage certifications and overseas exhibitions
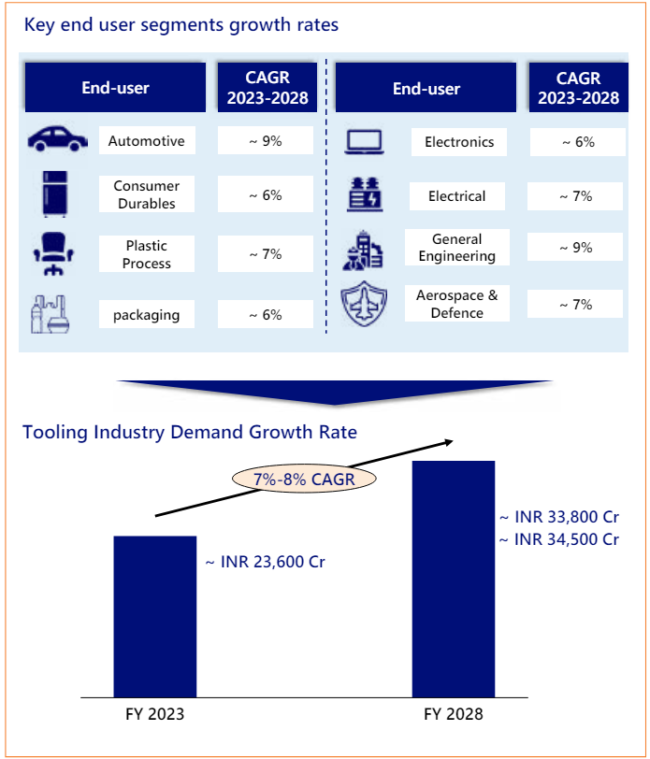
Source : Statista, Fortune India, NRI Analysis
Future estimations of tooling According to the report, the Indian tooling industry is estimated to grow at CAGR of ~7-8% by 2028 aligned to strong growth in key end-user segments. Between 2023 and 2028, it estimates the automotive end-user segment to grow at a CAGR of ~9%, consumer durables at ~ 6%, plastic process at ~ 7%, packaging at ~ 6%, electronics at ~ 6%, electricals at ~ 7%, general engineering at ~ 9%, and aerospace & defence at ~ 7%, respectively.
Key end user segments growth rates & Tooling Industry Demand Growth Rate
Challenges faced by tool rooms in India
Indian tool rooms grapple with many challenges. Let’s take a look at the ones that the report has highlighted:
Lack of industry-ready tool room courses:
In Indian Tool Room Training Centers (TRTC), students are trained in basic machining and assembly of moulds, but lack hands-on experience in advanced machinery and, thus are not industry-ready. Outside India, long-term courses with a focus on advanced tooling skills are common in Engineering Institutes, Colleges of Technology & specialized Vocational Centers
Lack of competitive salaries:
CTRs’ investment in workforce training does not pay the required dividends due to high instances of attrition of trained workforce to OEMs/ Tier-1 suppliers as well as non-manufacturing jobs in pursuit of better salaries, better work culture and bigger brand names. An average Indian toolmaker is underpaid compared to his Chinese, Korean or Japanese counterparts.
High cost of financing:
Even though Indian tool rooms want to expand their consumer base to new sectors like aerospace & medical equipment manufacturers, the need for high-precision equipment is an issue, as they are expensive to procure. Besides, the lack of low-cost finance hinders ITRs’ ability to invest in advanced tooling machinery, equipment & software for precision tools and moulds. Moreover, the challenges in furnishing formal data for credit assessment is an issue since accounting practices are not developed in some cases.
Lack of capital funding:
While global tool rooms have better access to capital funding, Indian tool rooms still face issues to avail of easy financing and subsidized loans.
Issues related to concurrent engineering
OEMs outsource to tool rooms post the designing stage. There is a lack of input/ concurrent engineering from tool rooms on the viability of the part. Due to this, the design for manufacturability shared with tool rooms is not viable, and requires one or more rounds of revision. Delayed manufacturing due to repeated redesigning, increases the lead time for tool rooms. To accommodate last-minute design modifications, numerous rounds of testing and rework are needed, making the delivery time of Indian tool rooms higher than imports.
Lack of outsourcing ecosystem
There is a low level of collaboration due to the dispersed presence of tooling suppliers in India, whereas, overseas tool rooms are located close to design and manufacturing facilities, suppliers, etc., which creates an ecosystem enabling large-scale subcontracting. This also enables tool rooms to process large consignments with less delivery time by sharing capacity and capabilities.
Key imperatives
The Indian tooling industry is stuck in a loop of dependencies, which restrict the development and betterment of ITRs. Attaining excellence in manufacturing and robust project execution are key steps towards improving the state of ITRs. However, it is important to control the costs incurred. Once the cost is under control, increased customer confidence will help in winning new projects/repeat orders. Besides, improvement in capabilities can further augment asset utilisation and help in winning new projects too.
Disclaimer: This article was taken from TAGMA Times(December Edition 2023)
COMMENTS