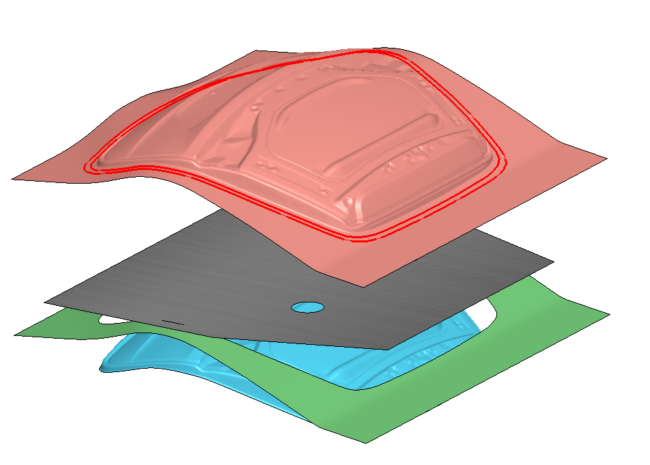
Troy, Michigan: Engineering Technology Associates, Inc. (ETA) proudly announces the launch of Dynaform 7.2, the latest version of their leading sheet metal forming simulation software. Building on the robust capabilities of its predecessor, Dynaform 7.2 introduces a range of new features and enhancements designed to further streamline and optimize the simulation of die system processes in the automotive, aerospace, and manufacturing sectors. This release marks another step forward in ETA’s commitment to providing state-of-the-art tools for engineers and manufacturers worldwide.
Dynaform 7.1 was groundbreaking in its own right, introducing advanced Die Face Design (DFD) and Formability Simulation (FS) capabilities. However, Dynaform 7.2 brings a host of new features aimed at improving the speed and precision of metal forming processes. Notable enhancements include improvements in Blank Size Engineering (BSE), Die Face Design (DFD), Formability Simulation (FS), and Tube Bending & Forming (TBF). The BSE module now offers better nesting results, providing users with higher material utilisation rates. The DFD module sees a boost in tool design flexibility with features like the Auto CAM and Trim Segment functionalities, which streamline multistage design and cutting operations.
ETA’s Sigform solver continues to be at the core of accurate and rapid multistage forming simulations, now further enhanced to deliver even more precise results under complex forming conditions. Moreover, the Die Structural Integrity (DSI) module ensures that die structures are analyzed dynamically, offering detailed insights into mechanical performance, load-bearing capacity, and potential areas of stress.
“We’re thrilled to unveil Dynaform 7.2, a significant leap forward in sheet metal forming simulation technology,” said Dr. Shan Nageswaran, CTO, ETA Inc. “This latest release builds upon the success of its predecessor, offering a broader range of features and enhancements that will empower engineers to optimize their processes and achieve unprecedented levels of efficiency and precision.”
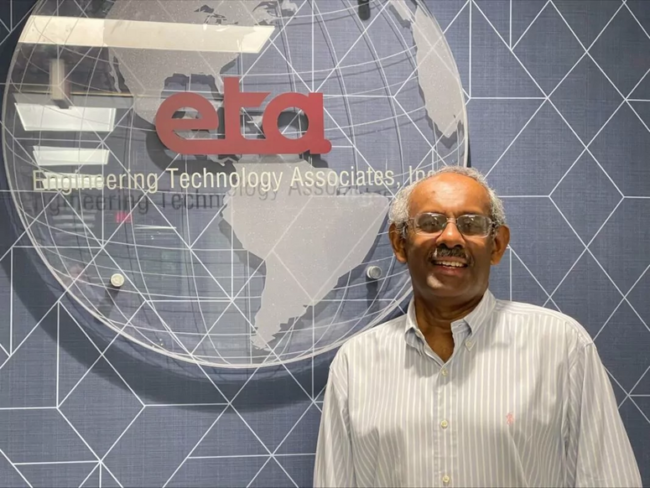
“With Dynaform 7.2, ETA continues to demonstrate its commitment to providing industry-leading solutions that drive innovation and productivity in the manufacturing sector,” added Dr Shan.
Key Features of Dynaform 7.2
Building on its predecessor, Dynaform 7.2 introduces several critical new features, making it the most comprehensive sheet metal forming solution to date. Here are the key highlights:
- Sigform Solver Enhancements: Dynaform 7.2’s Sigform provides even greater accuracy and efficiency in sheet metal forming simulations, supported by parallel frameworks that enable faster processing.
- Die Face Design: A series of new tools such as the Auto CAM, Trim Segment, and Flange Tool Enhancements make multistage die face design easier and more intuitive. Users can now perform operations like trimming, flange modification, and addendum creation with increased flexibility.
- Clamping Springback in FS: This feature allows for the measurement of springback using pads, pilot pins, and clamps, enabling sequential closing for improved simulation accuracy.
- Hot Forming in FS: With the growing application of high-strength steel, Dynaform 7.2 introduces a user-friendly interface for complex hot forming setups, simulating various stages from gravity and forming to cooling and hardening.
- Sheet Drop Test: Dynaform 7.2’s Drop Test module simulates part deformations during production, analyzing issues like panel deformations from drops, thus ensuring dimensional accuracy in automotive components.
- Die Structural Integrity (DSI): This module provides a comprehensive solution for die system analysis, offering insights into nonlinear, dynamic problems commonly encountered in mechanical and structural engineering.
With these advancements, Dynaform 7.2 offers a more integrated and efficient solution to the challenges of sheet metal forming, enabling users to reduce production time, minimize errors, and increase profitability. Whether it’s for automotive, aerospace, or other industrial applications, this latest release is set to redefine productivity and performance standards in the die-making process.
COMMENTS