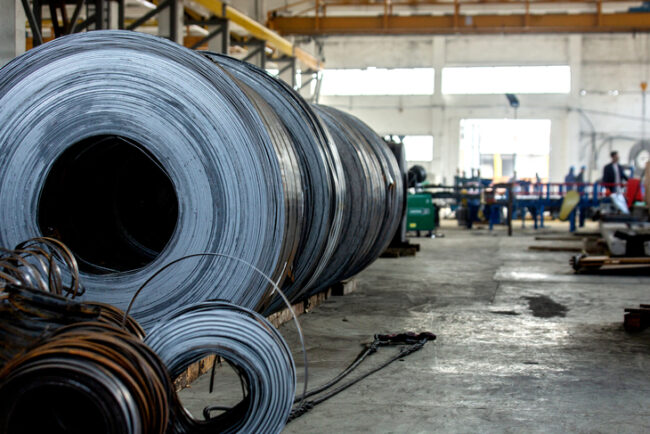
Did you know that Robert Forester Mushet, a British metallurgist and businessman, was credited with inventing the first commercial tool steel in 1868? Called R Mushet’s Special Steel (RMS), this tool steel was made by adding a small amount of tungsten to molten steel, which made it much harder than traditional steel. This allowed RMS to be used to make tools that could cut and shape harder metals than was possible before. RMS is considered one of the most important contributions to metallurgy in the 19th century. Today, tool steel has revolutionized the manufacturing industry, which now boasts stronger, more durable, efficient and long-lasting machine tools, blades, and drills.
The tool steel market in India is projected to grow from USD 369.74 million in 2023 to USD 647.30 million by 2032, at a Compound Annual Growth Rate (CAGR) of 6.42%, reveals the findings of a Credence Research report on the Indian tool steel industry published earlier this year. Over the past few years, India’s tool steel market has witnessed significant growth, driven by the increasing demand from application industries and a growing focus on manufacturing high-quality, precision components.
The tool steel market in India is characterized by the presence of domestic as well as international players. Playing the role of an enabler of product innovation and quality improvement, the tool steel market caters to the ever-evolving requirements of various sectors including automotive, manufacturing, construction, and heavy industry, among others. In terms of value and volume, the market has been expanding steadily, with projections indicating a continued positive trajectory. This growth is underpinned by the increasing demand from end-use industries, investment in infrastructure development, and the growing automotive sector in India, highlights the report.
Significance of tool steel in the tooling industry
In recent years, the Indian tooling industry has experienced significant growth and transformation, driven by factors including increasing industrialization, infrastructure development, and the expansion of key sectors such as automotive, aerospace, and manufacturing. Tool steel plays a crucial role in this ecosystem, serving as the backbone of tool and die manufacturing, mould making, and precision engineering applications.
T. Gopalakrishnan, Director – Marketing, Multiple Special Steel Pvt. Ltd. says, “The current trends and demands in the industry prominently revolve around diversification, technology adoption, localisation, and the exploration of newer manufacturing methodologies. Companies are actively seeking ways to broaden their scope, integrate advanced technologies, localise production, and embrace innovative manufacturing approaches to stay ahead in the competitive landscape. Looking forward, the business outlook appears highly promising. The industry is on an upward trajectory, witnessing increased demand for domestic tools not only from the automotive sector but also from emerging industries such as aerospace, defence, electrical & electronics, and toy making. This diversification points towards sustained growth, presenting both opportunities and challenges for industry players.”
Tool steel serves as the foundation of tooling applications. In India, it is extensively used in the production of dies, moulds, and various precision components required in manufacturing processes across industries. Moreover, with the increasing demand for high-quality manufactured goods, there is a growing need for tool steels with superior properties to meet the evolving requirements of modern manufacturing. Indian tooling companies are increasingly turning to advanced tool steel alloys that offer enhanced performance, durability, and precision to optimize production processes. They are also using certified tool steel grades, advanced heat treatment processes, and rigorous testing and inspection protocols to maintain consistent quality standards and meet customer requirements.
The Indian tooling industry is also witnessing a trend towards customization and specialization, with manufacturers developing tailored solutions to meet the specific needs of different applications and industries. This includes the development of specialized tool steel grades optimized for specific machining processes, tooling applications, and environmental conditions, thereby enhancing efficiency and productivity in manufacturing operations. Indian tooling companies are embracing advanced manufacturing technologies and processes such as CNC machining, additive manufacturing, and EDM (electrical discharge machining), among others, to stay competitive in the global market.
The integration of digitalization and Industry 4.0 technologies is reshaping the Indian tooling industry, enabling manufacturers to streamline production processes, optimize resource utilization, and enhance decision-making capabilities. This includes the use of digital twins, IoT (Internet of Things) sensors, AI (Artificial Intelligence), and predictive analytics to monitor tooling performance, optimize maintenance schedules, and minimize downtime in manufacturing operations.
Vishal Purohit, Director, Purohit Steel India Pvt. Ltd. says, “Post-COVID, the markets are gradually recovering at a cautious pace; the trajectory is set to become more dynamic and innovative. Anticipated growth signals a promising decade ahead, characterised by increased innovation and potential expansion in various sectors. The industry has seen steady growth due to increased demand from sectors like automotive, electronics, and manufacturing. With technological advancements, especially in automation and 3D printing, there’s potential for further growth.”
Tool steel: Properties and scope
Tool steel is made using various carbide-forming materials. The prominent ones are tungsten, vanadium, molybdenum, and chromium. Based on the type of application, there have been instances of cobalt or nickel also being used to make tool steel.
This adaptable metal alloy is used in moulds for plastic injection moulding machines, blades for lathes, punches and dies, etc. Its properties like high wear resistance and increased strength when heated at high temperatures have made it popular. Besides, tool steel has minimal trace elements, a good tolerance limit, and is adaptable to comply with etch-graining and polishing.
“When used in plastic moulding applications, tool steels offer excellent machinability, polish ability, homogeneity, low Sulphur content, and a good photo etching ability. They also exhibit better toughness and weldability than other counterparts. They also have a high material removal rate, thus making them ideal for usage in high cavity designs,” states a recently published Polaris Market Research report.
In addition, tool steel is easy to machine, which makes it a cost-effective material to use in manufacturing. All these factors have broadened the scope for tool steel.
Types of tool steel
Tool steel is classified into various grades. Each type has unique properties that are suited for specific applications. Let’s take a look at some common grades:
- A2 Tool Steel: A2 tool steel is an air-hardening, medium-alloy, cold-work tool steel known for its excellent toughness and wear resistance. It is often used for blanking, forming, and trimming dies, as well as punches and shear blades.
- D2 Tool Steel: D2 tool steel is a high-carbon, high-chromium, air-hardening tool steel known for its exceptional wear resistance and good hardness retention. It is commonly used for forming dies, punches, and shear blades, as well as for making industrial knives and cold work tooling.
- O1 Tool Steel: O1 tool steel is a general-purpose oil-hardening tool steel with good durability, wear resistance, and machinability. It is suitable for a wide range of applications including forming dies, punches, gauges, and woodworking tools.
- S7 Tool Steel: S7 tool steel is an air-hardening shock-resistant tool steel known for its high impact toughness and excellent wear resistance. It is often used for forming and trimming dies, chisels, pneumatic tools, and cold work tooling subjected to high-impact loads.
- H13 Tool Steel: H13 tool steel is a hot-work tool steel characterized by its high toughness, heat resistance, and wear resistance. It is widely used for die casting dies, extrusion dies, forging dies, and hot shear blades in applications involving high-temperature operations.
- P20 Tool Steel: P20 tool steel, also known as plastic mould steel, is a pre-hardened, low-alloy tool steel widely used in injection mould and extrusion mould applications. It offers good polishability, machinability, and dimensional stability, making it suitable for producing plastic parts with high precision.
Based on the specific production needs, tool steel manufacturers help their clients make informed choices about “selecting the most suitable and efficient tool steel that will minimize progressive damage caused by cyclic mechanical loading and other factors. These companies offer various tool steel grades to address failure mechanisms such as abrasive wear, adhesive wear, breakage, and chipping. By doing so, they help clients to enhance their overall manufacturing process and increase productivity by minimizing the occurrence of failure mechanisms”, explains the Polaris Market Research report.
Market opportunities
Developing economies could present opportunities for the tool steel market. Let’s understand how. By developing tool steel variants tailored for specific applications, such as high-temperature or corrosion-resistant grades, they can potentially meet the unique needs of various industries.
Besides, investing in R&D to produce new grades of tool steel with enhanced properties could open up new applications and markets, while leveraging advancements in 3D printing and precision machining to produce tool steel components could enhance market penetration. In fact, collaborations with tool and die manufacturers can promote innovation and ensure the development of optimized steel grades.
It is well known that tool steel is used in the manufacturing of a variety of automotive components; the gradual shift towards electric vehicles and the need for advanced manufacturing tools in this sector present a growing market for tool steel. “The automobile sector, especially EVs, will most likely provide opportunities for the Indian tooling industry in time to come,” says Raju Tolani, Managing Director, Swiss Steel India.
Also, emphasizing the recyclability and environmental benefits of tool steel can attract industries that focus on sustainable manufacturing practices.
Future outlook
Overall, the tool steel industry in India continues to play a vital role in supporting the country’s industrial growth and competitiveness on the global stage. With ongoing advancements in technology, quality, and market outreach, Indian tool steel manufacturers are well-positioned to capitalize on emerging opportunities and contribute to the nation’s economic development.
Image Credit: Purohit Steels
COMMENTS