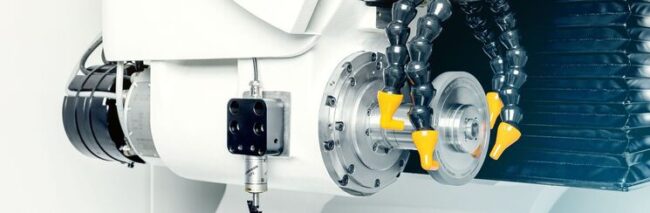
You don’t even want to consider machine downtimes – except when it is planned. That is why many manufacturers keep production running flat out for long periods – especially when machines run reliably from the start. But machines do need care. Failure to miss the first signs of wear can lead to machine downtimes and end up being very expensive. Machine health checks are known as preventive maintenance and are carried out by experienced technicians. But what exactly happens when our technicians put machines through their paces?
One central element of preventive maintenance is checking the machine geometry. Because this can be adversely affected over time. That is why, after an initial visual inspection of the machine, our experienced technicians check the status of the machine geometry. Any values that do not meet specifications will affect the precision of machine operation. Using the example of a WALTER HELITRONIC tool grinding machine, we will explain to you what this test involves in detail:
- Workpiece Carrier Runout Condition
The technician determines the concentricity of the holder and checks the runout using the A-axis test bar. Excessive runout leads to wobbling tools, in-dexing errors, and other problems during tool machining.
- Parallelism of the A-axis to the X-axis
Using a test bar, the technician measures the geometry of the A-axis relative to the X-axis and adjusts the zero point and centerline if necessary.
- Parallelism of the Z-axis
The technician checks the parallelism of the Z-axis using a granite block. They remove one of the guide shoes from the guide rails to check its condition, pretension and play. Poor guide rails are a common cause of a misaligned Z-axis.
- Perpendicularity of Y-axis to the Top Plate
If the Y-axis tilts forward, the rails are worn. In this case, the technician makes adjustments to the tool program.
- Perpendicularity of the Wheelhead to the Top Plate
To prevent premature wear of the ball screws, the technician aligns the Y-position of the castings in the guideways.
Further Priorities of Preventative Maintenance
The checks also include the inspection of electrical components and safety devices. The control cabinet is inspected and batteries replaced if necessary. The technician measures the temperature with a sensor that is very sensitive to small fluctuations in temperature. The temperature of the electrical compo-nents in the cabinets must remain below 55°C. Here is an example of a cost calculation: if a capacitor overheats because a fan is not working, the CNC control unit may burn out. This incurs costs amounting to tens of thousands of euros. However, replacing the blower before it fails only costs a three-digit figure.
Continuing with the test process: the technician now checks the emergency stop circuit and door locks. The list of tasks also includes replacing wear parts and an oil change. The A-axis and C-axis are also checked as well as the pretension of the gears. Finally, the machine is recalibrated.
The health check is now complete. The technician then documents everything in a maintenance report and notes recommendations for future actions.
Extending the Service Life of Machines
Nobody knows a machine better than the team that built it. When certified technicians look into the heart of a machine, they know exactly what they are looking for at every test point. They take the right measures to ensure that the machine delivers accurate and repeatable results. This allows machine operators to concentrate fully on their actual tasks. And they can be sure that the machine is in good condition and has the endurance to run smoothly until the next inspection.
But when is the next inspection required? You decide whether you want a one-off or recurring inspection: it’s up to you. We recommend intervals of 4, 6, 12, 18 or 24 months, depending on which schedule is best suited to the respective machine’s running hours. Please ask your technician for advice.
Article Courtesy – United Grinding Group
COMMENTS